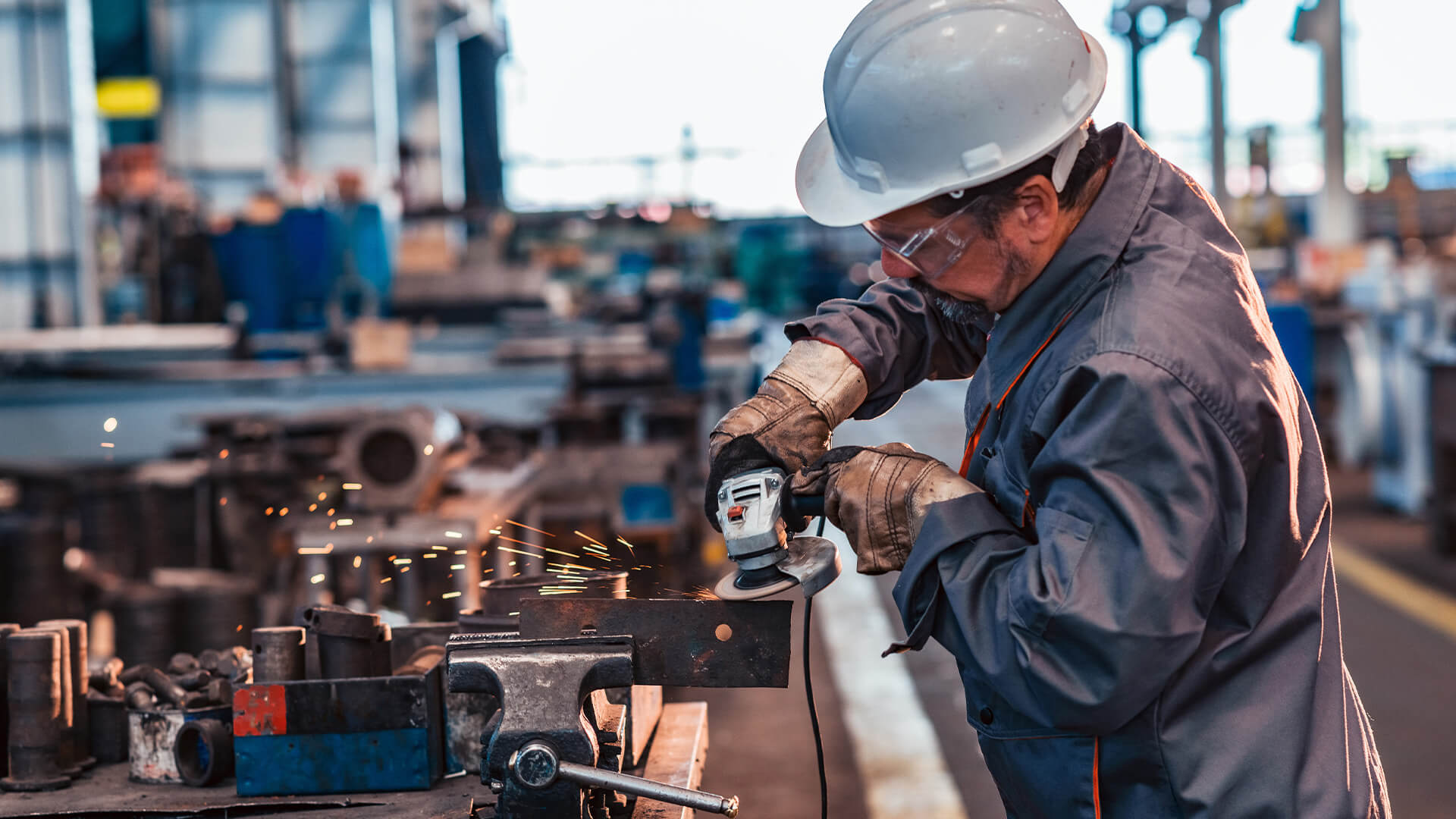
Keeping your budget in check and making savings wherever possible is important if you run a business, and manufacturing firms have a particular need to minimize unnecessary expenses if they want to compete with the big players.
To that end, here are some tips and strategies for saving money as a small manufacturing firm in the US that will have a tangible impact on your bottom line.
Purchasing used machinery
An easy way to save thousands is to avoid ordering brand new equipment and instead make the switch to sourcing heavy duty gear from the second hand market.
Today it’s a breeze to find high quality items of all kinds, whether you need a used waterjet cutting machine, a lathe, a CNC mill, a 3D printer or anything in between.
Obviously, you need to be a bit more vigilant when buying second-hand manufacturing equipment, as things like maintenance and hours used will come into play in determining the value of a given unit. Even so, with a bit of research and the use of reputable machinery marketplaces, this will let you innovate and accelerate production without paying through the nose.
Digitizing key processes
Moving from analog to digital can turbo charge productivity and deliver a raft of other benefits as well, such as streamlining decision-making and lessening the likelihood of accidents occurring in a manufacturing environment.
There are a few options for digitization available to you, most of which focus on taking the use of physical paper documents out of the equation, and instead relying on their digital equivalents wherever possible.
From work instructions to customer invoices, going digital and kicking paper to the curb has myriad benefits, and is worth doing sooner rather than later.
Limiting waste
Material costs have risen rapidly in recent years, and so driving down waste on the production line can save money as well as time.
Focusing on refining your approach to quality control throughout every step of the process is important for this reason. The more attention to detail is given to quality, the fewer components and products will be rejected because of the presence of flaws.
Once again, digital tech rides to the rescue here, as you can implement all sorts of systems and solutions to manage QC in an automated way, easing pressure on your staffing resources and allowing you to be proactive in reducing material waste.
Embracing workplace safety
Cutting corners when it comes to safety is a false economy, as well as being ethically unsound as a practice. If employees are injured in the line of duty, they won’t be able to fulfill their roles, and you’ll have to pay to find replacements, which is tricky if there is a shortage of skilled workers with their particular training and experience.
Conversely, if you are up to speed with the latest health and safety guidelines and regulations, you will be able to manage your manufacturing operations with a view to keeping every person well protected while they are on site.
Providing adequate training to employees that have direct use of heavy machinery is part of this, but you also need to equip them with the right protective gear in hazardous scenarios, as well as making sure that they have enough time in the day to hit production targets, and are not forced to skip safety steps because of unachievable deadlines.
Adopting preventative maintenance
Lastly, when it comes to keeping your facility ticking over consistently and maintaining the desired level of output from day to day, preventative maintenance techniques are king.
The equipment you use will always undergo a degree of wear and tear over time, and choosing to look out for signs of this and take steps to remedy problems before they can spiral out of control will lessen the chances of unplanned downtime.
There are several layers to preventative maintenance, from visual inspections of equipment to full-blown AI-powered monitoring. Even making simple changes to your maintenance schedules can be majorly advantageous to your entire organization.
So all that remains is for you to look at your current strategies and see if cost-saving revisions are needed in light of what you’ve learned here.